Introduction
In the metal industry, accurate material identification and sorting are crucial to ensuring product quality, compliance with standards, and operational efficiency. Optical spectrometers play a key role in these processes, enabling rapid, precise, and non-destructive analysis of metals and alloys. From recycling scrap metal to quality assurance in manufacturing, spectrometry helps industries maintain material integrity and improve sustainability.
This blog explores how optical spectrometers enhance material identification, sorting, and quality control, along with their benefits across various industries.
Material Identification and Sorting
Material Identification
Alloy Identification

- Purpose: Different industries, such as aerospace, automotive, and construction, rely on various metal alloys, each with specific properties. Correctly identifying alloys ensures performance under required conditions (e.g., strength, corrosion resistance, conductivity).
- How It Works: Optical spectrometers analyze the light emitted or absorbed by a metal sample when exposed to a specific energy source. Each element has a unique spectral fingerprint, allowing precise identification of its composition.
- Example: A spectrometer can distinguish between stainless steel grades (e.g., 304 vs. 316) by detecting slight differences in chromium and nickel content, which impact corrosion resistance and mechanical strength.
Material Sorting
Scrap Metal Sorting
- Purpose: In recycling and waste management, proper metal separation prevents contamination and ensures high-quality recycled materials.
- How It Works: Optical spectrometers quickly analyze scrap metal compositions, allowing automated systems to direct metals into appropriate recycling streams.
- Example: A spectrometer distinguishes aluminum alloys such as 6061 or 7075, ensuring that sorted scrap meets quality specifications for reuse.
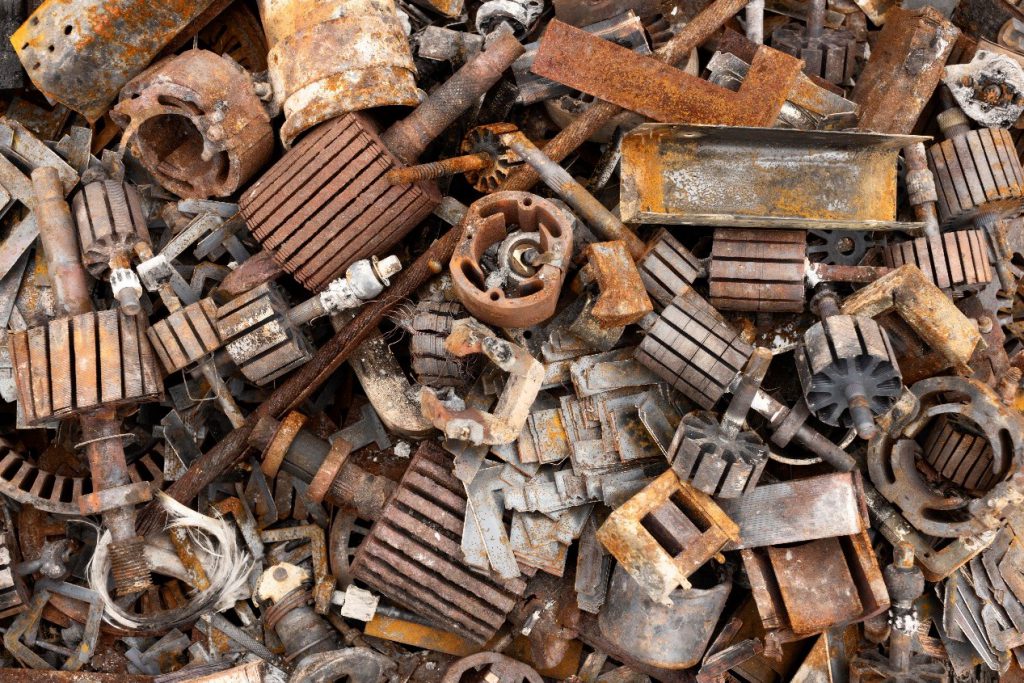
Scrap Metal Sorting Process
- Collection & Preparation: Scrap is gathered from industrial waste, construction debris, and consumer electronics. It is then processed (shredding, shearing, or baling) and contaminants are removed.
- Identification & Sorting:
- Spectral Analysis: Spectrometers analyze metal samples via laser or spark discharge to identify their composition.
- Real-Time Sorting: Automated conveyor systems or handheld spectrometers direct metals into the appropriate recycling stream.
- Processing & Recycling: Sorted metals are melted, refined, and repurposed into new products.
Benefits of Using Optical Spectrometers in Sorting
- Accuracy & Precision: Ensures correct material classification, reducing contamination.
- Speed & Efficiency: Enables high-throughput sorting, improving productivity.
- Cost Savings: Reduces reprocessing needs, saving time and resources.
- Environmental Benefits: Promotes sustainability by reducing the need for virgin raw materials and minimizing waste.
Quality Control and Assurance
Verification of Raw Materials
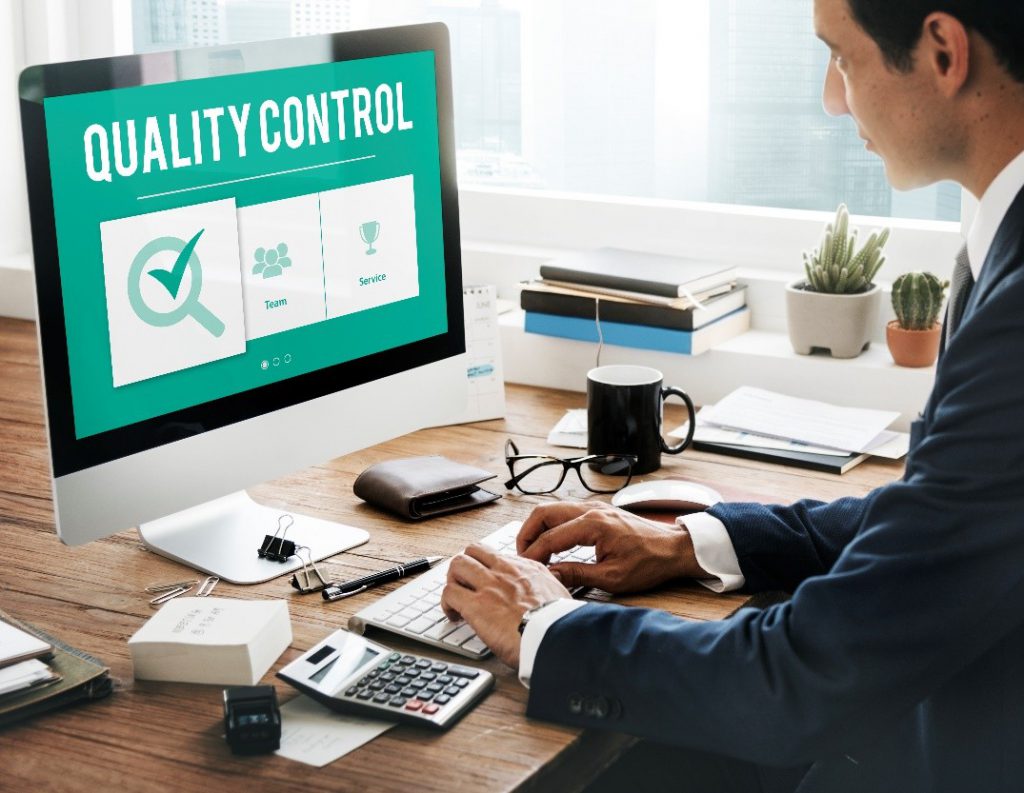
- Purpose: Ensures incoming materials meet specifications before production begins, preventing defects and non-compliance.
- How It Works: Spectrometers analyze raw metal samples, confirming their elemental composition against required standards.
- Example: Stainless steel production requires precise chromium and nickel levels for corrosion resistance.
In-Process Monitoring
- Purpose: Continuously monitors metal composition during manufacturing to maintain quality.
- How It Works: Spectrometers integrate with production lines to provide real-time analysis, preventing defects.
- Example: In steel mills, spectrometers track molten steel composition to ensure adherence to specifications.
Final Product Inspection
- Purpose: Ensures that finished metal products meet industry standards before shipment.
- How It Works: Spectrometers verify composition, preventing defective materials from reaching the market.
- Example: In aerospace, turbine blades are tested to ensure high-temperature durability.
Benefits of Optical Spectrometers in Quality Control
- High Precision: Detects small variations that could affect product performance.
- Non-Destructive Testing: Allows inspection without damaging samples.
- Real-Time Monitoring: Enables immediate corrections, reducing waste.
- Compliance Assurance: Meets ASTM, ISO, and DIN standards.
- Enhanced Product Quality: Ensures consistency and reliability.
- Cost Reduction: Prevents rework, scrap, and product recalls.
Industry-Specific Applications
- Aerospace: Ensures high-strength titanium and aluminum alloys meet stringent safety requirements.
- Automotive: Verifies metal compositions for structural integrity and performance.
- Medical Devices: Confirms biocompatibility of titanium and cobalt-chrome alloys.
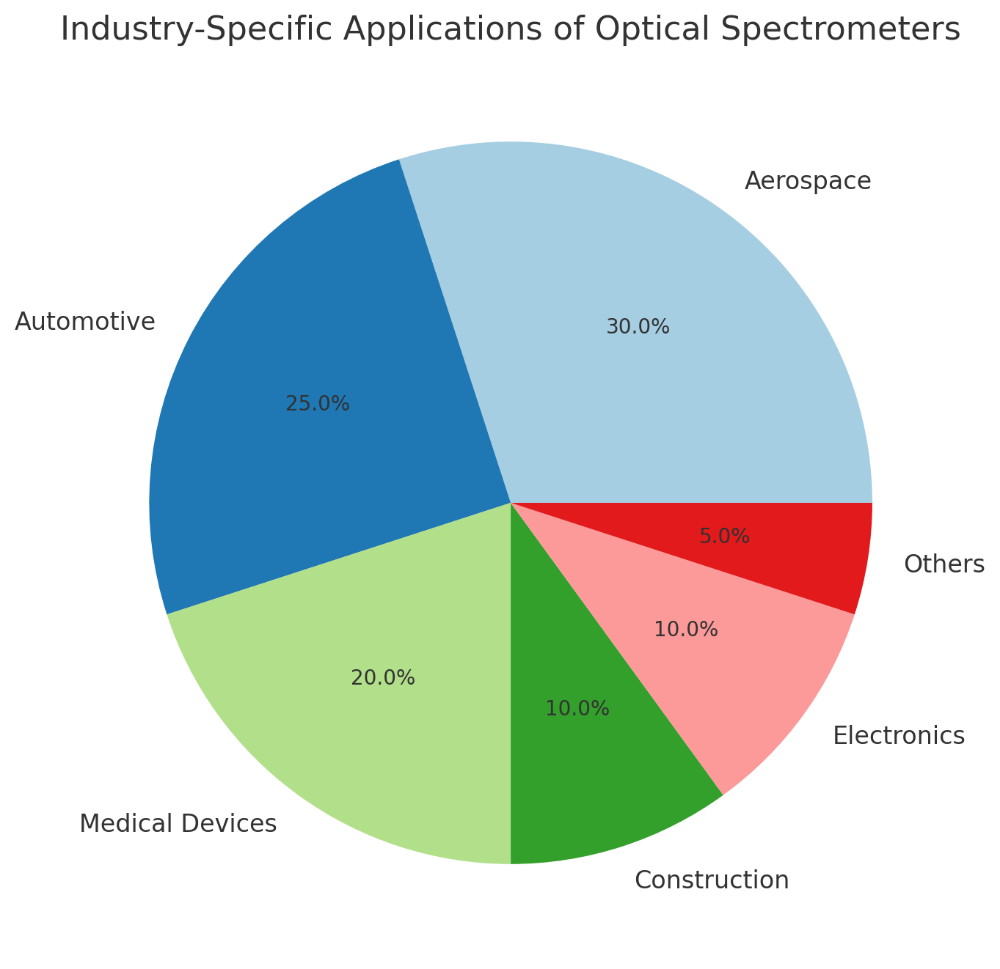
Conclusion
Optical spectrometry plays a vital role in modern metal processing, from accurate material identification to efficient sorting and stringent quality control. Its ability to provide precise, real-time, and non-destructive analysis enhances operational efficiency, reduces costs, and promotes sustainability.
With industries demanding higher accuracy and compliance with strict standards, investing in optical spectrometry is not just an option but a necessity for maintaining competitiveness and ensuring product reliability.