“Standards and Science: Why Nitrogen Limits Matter in TMT Bar Manufacturing”
1. Introduction
1.1 Overview of TMT Bars
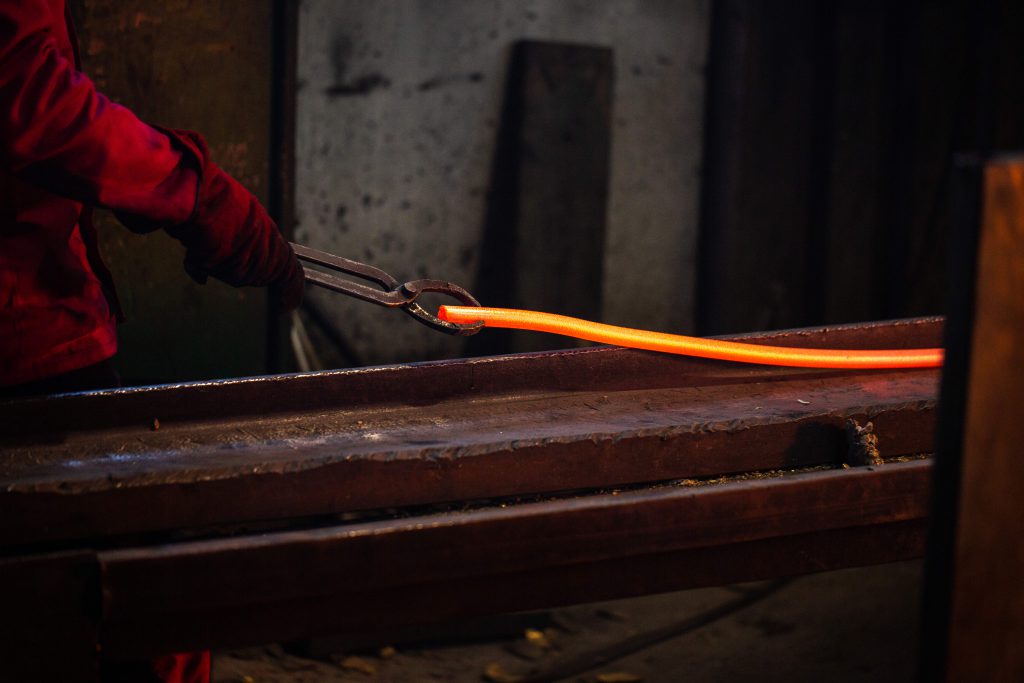
Thermo-Mechanically Treated (TMT) bars are a crucial component in reinforced concrete structures, providing high strength, flexibility, and durability. Their quality is determined by their chemical composition and mechanical properties.
1.2 Importance of Chemical Composition in TMT Bars
The performance of TMT bars depends significantly on their chemical constituents. Elements like carbon, manganese, sulphur, phosphorus, and nitrogen play a critical role in determining the mechanical properties of steel.
Element | Typical Range (%) | Role in TMT Bars | Effects of Excess/Deficiency |
Carbon (C) | 0.15 – 0.25 | Increases strength and hardness | Excess reduces ductility and weldability |
Manganese (Mn) | 0.5 – 1.0 | Improves toughness and wear resistance | Excess causes cracking and brittleness |
Sulphur (S) | ≤ 0.05 | Enhances machinability | Excess makes bars brittle |
Phosphorus (P) | ≤ 0.05 | Improves strength and corrosion resistance | High levels reduce toughness and ductility |
Silicon (Si) | 0.1 – 0.4 | Increases strength and shock resistance | Excess can make bars too rigid |
Chromium (Cr) | 0.1 – 0.3 | Provides corrosion resistance | Excess increases hardness but reduces weldability |
Nickel (Ni) | 0.1 – 0.3 | Improves toughness and corrosion resistance | High levels increase cost without major benefits |
Copper (Cu) | 0.2 – 0.4 | Enhances corrosion resistance | Excess may cause hot shortness (brittleness at high temperatures) |
Vanadium (V) | 0.05 – 0.15 | Helps in grain refinement, improving strength | Excess reduces ductility |
Niobium (Nb) | 0.01 – 0.05 | Improves yield strength and toughness | Excess can cause embrittlement |
Nitrogen (N) | ≤ 0.01 | Enhances strength and hardness in controlled amounts | High levels cause brittleness and aging effects |
1.3 Role of Nitrogen in Steel Manufacturing
Nitrogen (N) is an essential but often overlooked element in steel. While controlled amounts of nitrogen can enhance certain mechanical properties, excessive nitrogen can lead to embrittlement and cracking. Hence, monitoring and controlling nitrogen content in TMT bars is critical to ensuring their reliability and longevity.
2. Effect of Nitrogen in TMT Bars
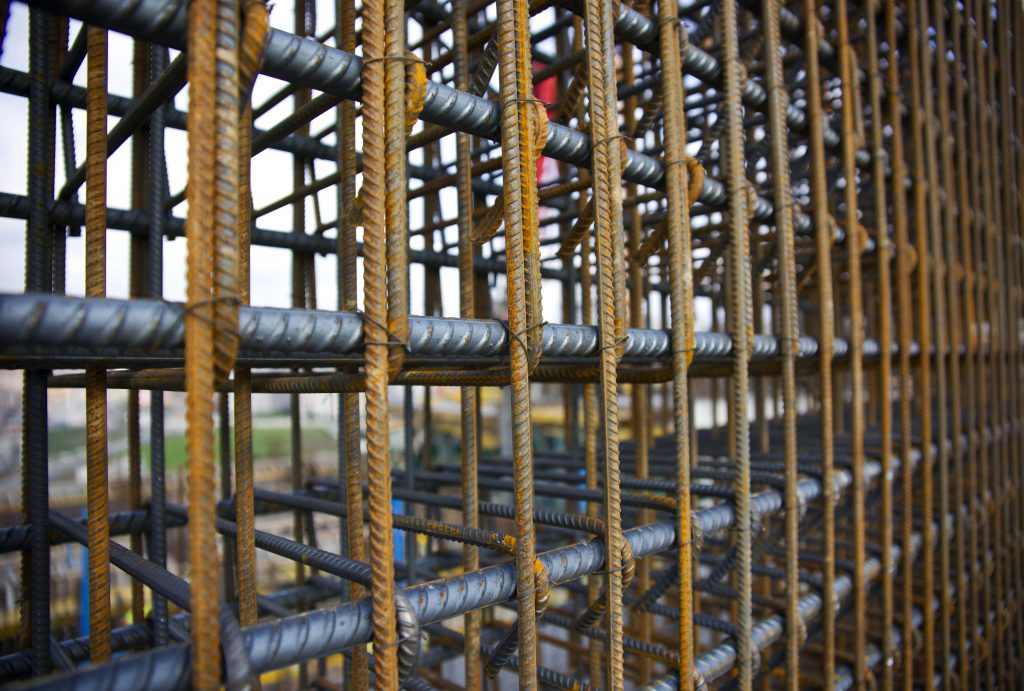
- Tensile Strength (MPa)
- Hardness (HV)
- Impact Resistance (J)
2.1 Benefits of Nitrogen in Steel
- Grain Refinement: Nitrogen in steel contributes to finer grain structures, improving strength and hardness.
- Increased Strength: Nitrogen in small amounts strengthens steel by forming nitrides with alloying elements.
- Enhanced Toughness: A controlled nitrogen level enhances impact resistance and wear properties.
2.2 Negative Effects of Excessive Nitrogen
- Brittleness and Cracking: Excess nitrogen can cause aging embrittlement, leading to structural failure over time.
- Reduced Ductility: High nitrogen content reduces the steel’s ability to deform without breaking.
- Poor Weldability: Nitrogen can form pores and cracks in welded joints, affecting structural integrity.
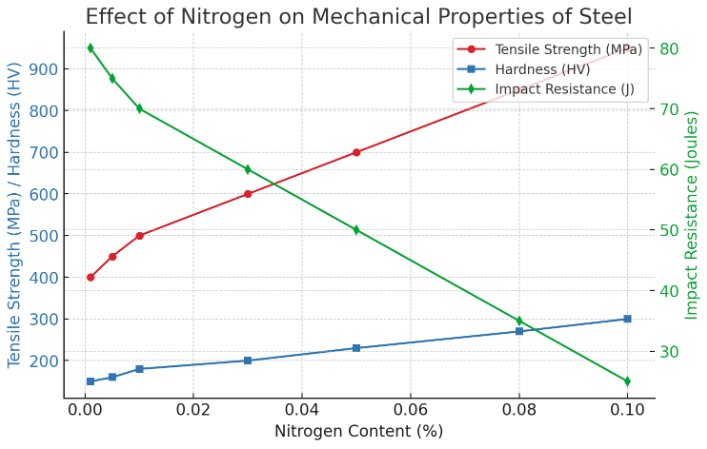
3. BIS and Other International Standards for Nitrogen in TMT Bars
3.1 BIS Standards (IS 1786:2008 & IS 2830:2012)
- IS 1786:2008 restricts nitrogen content to below 0.012% for superior weldability and toughness.
- IS 2830:2012 defines the acceptable nitrogen range for billet manufacturing.
3.2 International Standards Comparison
Steel Grade/Type | BIS Standard (IS) | ASTM Standard | ISO Standard | Permissible Nitrogen Limit (ppm) |
Mild Steel | IS 2062 | ASTM A36 | ISO 630 | 150 – 250 |
Low-Alloy Steel | IS 1786 | ASTM A572 | ISO 6935 | 120 – 200 |
Stainless Steel (304) | IS 6911 | ASTM A240 | ISO 15510 | 500 – 1000 |
Stainless Steel (316) | IS 6911 | ASTM A240 | ISO 15510 | 600 – 1200 |
High-Strength Steel | IS 15914 | ASTM A514 | ISO 4950 | 100 – 180 |
4. Methods for Nitrogen Analysis in TMT Bars
4.1 Optical Emission Spectroscopy (OES)
- Fast and precise, widely used in steel industries.
4.2 ONH Analyzer
- Measures Oxygen (O), Nitrogen (N), and Hydrogen (H) in steel, ensuring precise nitrogen content determination.
Method | Principle | Advantages | Limitations |
Optical Emission Spectroscopy (OES) | Excites metal samples using an electric arc/spark and analyzes emitted light spectra to determine nitrogen content. | Fast, precise, widely used in steel industries. | Requires proper calibration for accurate nitrogen measurement. |
ONH Analyzer | Measures Oxygen (O), Nitrogen (N), and Hydrogen (H) in steel using inert gas fusion, ensuring precise nitrogen content determination. | Highly accurate for trace nitrogen detection. | Requires specialized equipment and is time-consuming. |
5. Impact of Nitrogen Control on TMT Bar Quality
5.1 Strength and Ductility Balance
- Maintaining nitrogen within BIS-recommended limits ensures an optimal balance of strength and flexibility.
5.2 Corrosion Resistance & Weldability
- Controlled nitrogen prevents microstructural defects, improving corrosion resistance and weldability.
5.3 Effect on Fatigue Life of Reinforced Structures
- High nitrogen content can lead to premature fatigue failure, reducing structural lifespan.
6. Challenges in Nitrogen Control during Steel Manufacturing
6.1 Raw Material Influence
- Scrap steel may introduce higher nitrogen levels, requiring careful material selection.
6.2 Process Control in EAF & BOF
- Gas absorption during melting and refining must be minimized through optimized process control.
6.3 Role of Ferroalloys in Nitrogen Introduction
- Proper composition adjustments are needed to prevent excess nitrogen.
7. Conclusion
7.1 Summary of Findings
- Nitrogen plays a dual role in TMT bar quality—beneficial in controlled amounts but harmful in excess.
- BIS and international standards provide strict nitrogen limits.
- Advanced analytical methods like OES and IGF ensure precise nitrogen control.
7.2 Best Practices for Maintaining Nitrogen Levels
- Use high-quality raw materials with minimal nitrogen contamination.
- Implement strict process control.
- Conduct regular quality checks.
7.3 Future Trends in Steel Manufacturing for Improved Nitrogen Control
- AI-driven process monitoring for better nitrogen management.
- Enhanced refining techniques to reduce nitrogen in recycled steel.
- Real-time nitrogen analysis with advanced spectrometric techniques.
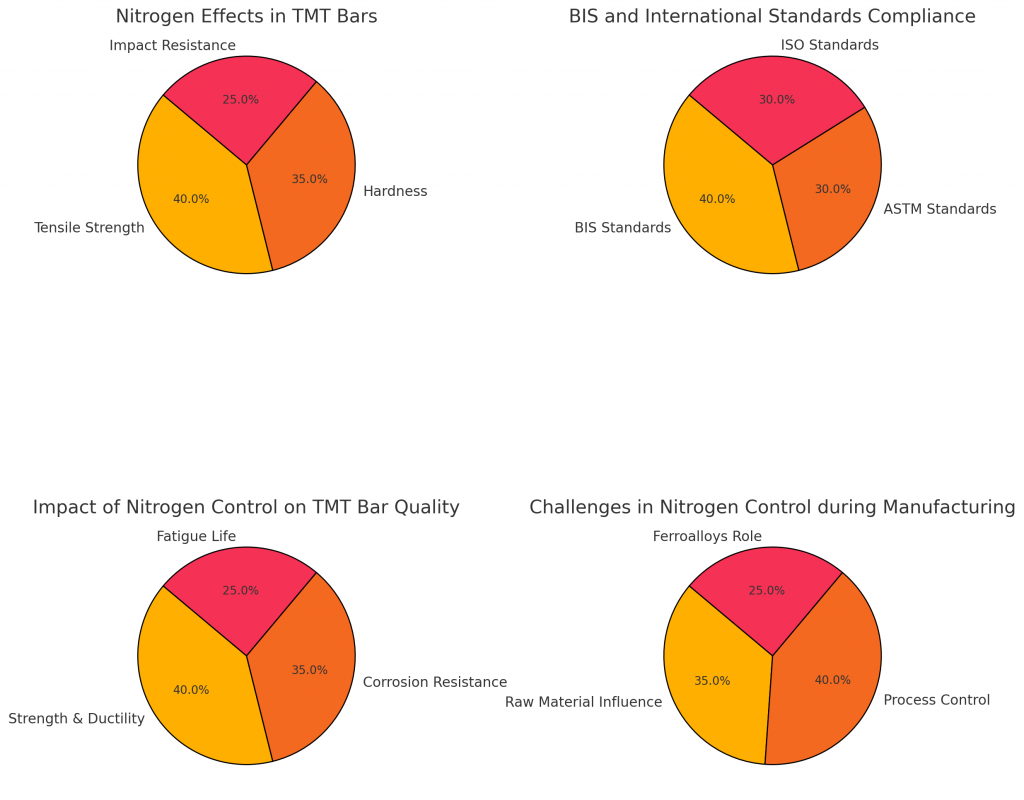